הקדמה
זהו פוסט עדכון אחרי הפוסט הקודם שלי "בדרך להרכבת SMT". קניתי את הכלים כדי שתהיה לי אפשרות לייצר כרטיסים אלקטרוניים. למדתי המון. לפעמים בדרך הקשה. בפוסט זה אסביר לכם מה באמת צריך כדי לייצר כרטיסים. ממה אפשר להימנע וטיפים לתוצאות טובות יותר בתהליכי ייצור של אב-טיפוס וסדרות קטנות.אני לא מומחה גדול לכל זה. אפשר כנראה להגדיר אותי כמתחיל בתחום. אבל עברתי מ-0 למצב שאני יכול לייצר מעגלים אצלי בחדר. כותב מהניסיון, כל עוד הדברים טריים בזכרון. אני בטוח שזה יעזור לחלק מהקוראים, אם רק הייתי מוצא פוסט כזה לפני שהתחלתי בתהליך הזה, כנראה שהייתי עושה כמה דברים קצת אחרת.
קצת פרטים לאלה שלא קראו את הפוסט הקודם, וגם כדי לרענן את הזיכרון:
- יש לי כמה רעיונות שזקוקים ליכולת ייצור כרטיסים אלקטרוניים
- בנוסף לרעיונות, בגלל מצב השוק (קורונה, מחסור ברכיבים), היתה מחשבה של "אם רק היתה לי יכולת לייצר את המוצרים האלה בעצמי"...
- קניתי את הציוד הדרוש כדי לעשות זאת
- שרדתי כדי לספר
אגב, היום כבר אין מחסור רכיבים ושכחנו את תקופת הקורונה, אבל יש את המכסים של טראמפ שהקפיצו כמעט את כל המחירים של הספקים (שרובם מארה"ב). אותו מתאם RS485 שהזכרתי בפוסט הקודם עולה היום $1 יותר.
יש מוצרים שהמכסים גרמו להקפצת מחיר בין 50 ל-100%.
מה שמייצר מצב בו עדיף לקנות דברים ישירות מסין כדי לא לשלם את המכסים שחברות אמריקאיות משלמות כדי לקבל רכיבים (שרובם מיוצרים בסין) ומוכרות אותן לחו"ל (אלינו).
וזה עוד יותר מדרבן אותי לייצר דברים בעצמי כדי להיות פחות תלוי בשרשרת האספקה הלא הגיונית הזו.
ואם תהיה יכולת ייצור, אולי אוכל גם להציע שירות הרכבה ללקוחות? (ספויילר: כנראה לא בזמן הקרוב).
בפוסט זה אני מתייחס רק לייצור עצמי של המעגלים, כי זה מה שאני רוצה לעשות. זה לא אומר שאי אפשר להשתמש בשירותי PCBA הזמינים היום כמעט מכל מפעל ייצור לוחות PCB.
בואו נתחיל בהסבר מה הם שלבי הייצור ולמה לא כדאי לדלג על שלבים אלה.
שלבי הייצור
כאשר מייצרים מעגל או מוצר, התהליך כולל מספר שלבים מרכזיים: אב-טיפוס, ייצור סדרתי קטן וייצור המוני.אב-טיפוס
בשלב אב-טיפוס (Prototype) מייצרים כמות קטנה של מעגלים כדי לוודא שהכל עובד כמו שצריך. במקרים בהם יש תיקונים, אין בזבוז גדול כי לא יצרנו כמויות גדולות שהולכות לפח.יצרני מעגלים מודפסים בסין מכריחים להזמין כפולות של 5 יחידות של אותו המעגל, וזה בדרך כלל מספר טוב להתחיל ממנו.
סדרה קטנה
אחרי שאב-טיפוס פועל כמצופה, אתם רוצים להיות מוכנים לייצר כמויות גדולות של המעגל. תלוי בגודל וסוג המעגל, אבל לרוב לטובת הייצור בכמויות מצרפים כמה מעגלים לפנל אחד כדי לנצל טוב יותר את התהליכים ואת יכולות המכונות. תהליך זה נקרא panelization.ושוב מייצרים כמות קטנה יחסית של הפנלים, שכוללים כמה מעגלים בתוכם.
למה כמות קטנה? כי לפעמים גם בתהליך זה יש טעויות. אולי צריך לסובב את המעגלים כדי לנצל טוב יותר את היכולות של המכונות. אולי צריך לרווח את המעגלים כדי שרכיבים לא יתנגשו כשהם צמודים אחד לשני (מחבר USB או מפסק בולטים מהלוח הם דוגמה קלאסית למקרים בהם הרכיב מתנגש ברכיב שנמצא בקצה השני של מעגל הבא על הפנל ואי אפשר להרכיב אותם יחד). אולי גם הכל רץ חלק ותרצו לנסות להגדיל את גודל הפנל כדי לסחוט עוד קצת יכולות מפס הייצור ולהיות מוכנים לשלב הבא.
יש הרבה שיכולים לכמות הכרטיסים בפנל אחד. אם רוצים לנצל את המקסימום מהתהליך, אז מנסים להכניס כמה שאפשר לתוך הגודל המקסימלי של הלוח שאפשר יהיה לייצר. אבל במקרים רבים זה לא השיקול היחיד.
אם אני לוקח את פרוייקט רכיבי ה-Plug-n-Play שאני עובד אליו, אז הרכבתי פנל של הבקר SAM21 (שגודל כל כרטיס הוא 88x55 מ"מ) כך שיהיו 4 מעגלים:
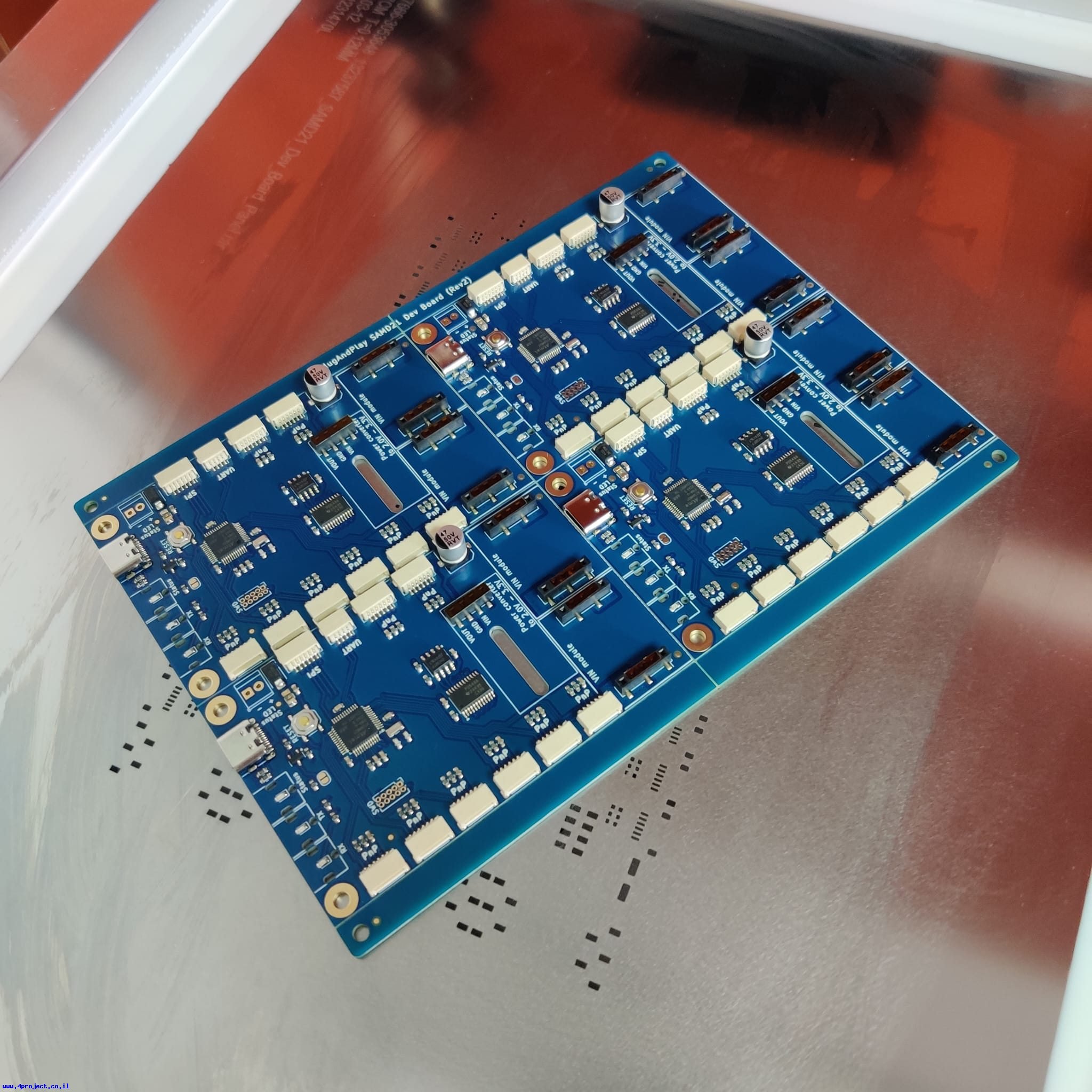
גודל הפנל הזה הוא בערך 19x15 ס"מ. ניסיתי לא לעבור את הגודל הזה בגלל מגבלה של התנור שיש לי. אפרט על כך בהמשך.
בפנל של מייצבי מתח לבקר יש 40 יחידות (כל כרטיס בגודל 14x12 מ"מ):
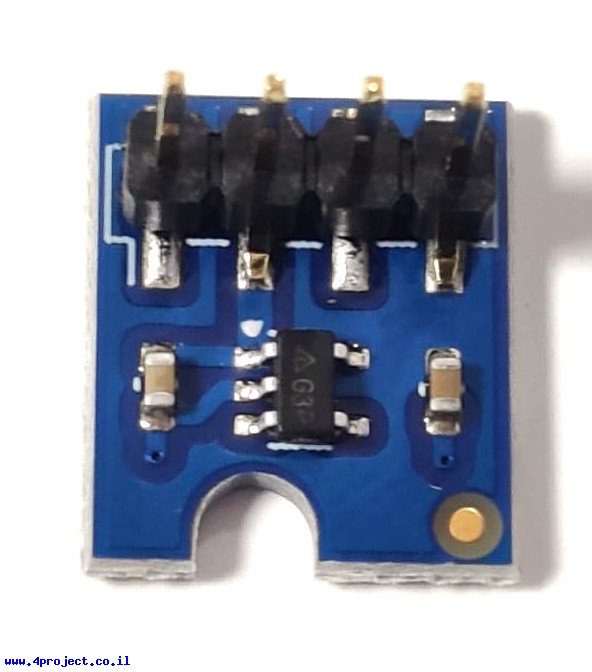
בסופו של דבר פנל של המייצבים הרבה יותר קטן מפנל של הבקרים (בערך 9x8 ס"מ) וטכנית הייתי יכול לעשות אותו גדול יותר, כך שהייצור יהיה אופטימלי יותר. אבל יש שיקולים אחרים שצריך להתחשב בהם. במקרה הזה לא יהיה לי מה לעשות עם יותר מדי מייצבים בלי הכרטיסים של הבקר. בינתיים היחס של 1 ל-10 היה נשמע לי הגיוני. צריך לייצר 10 פנלים של הבקרים ורק פנל אחד של המייצבים.
כמות הפנלים המיוצרת בשלב זה תלויה בצורך וכמויות שרוצים שיהיו במלאי. לרוב זה יהיה כמה עשרות פנלים.
ייצור המוני
זה השלב שלוקחים את התוצרים הבדוקים של שלב הסדרות הקטנות ולוחצים על הגז עד הסוף כדי לייצר כמויות גדולות מאוד של הכרטיסים.כמה גדולות? מאות ואלפים של הפנלים כל פעם.
כדי להתמודד עם ייצור כמויות כאלה צריך פס ייצור אוטומטי עד כמה שאפשר כדי שהתהליכים יתבצעו כמעט ללא מגע אדם ובאפקטיביות המקסימלית.
אני כנראה לא אגיע לשלב זה לעולם, לכן אני לא מכוון לשם גם מבחינת הכלים שקניתי. לדעתי גם היצרנים כמו Pololu, SparkFun ו-Adafruit לא נמצאים שם. עם מגוון כל כך גדול של המוצרים שהם מייצרים אני בספק אם הם מייצרים יותר מכמה עשרות פנלים בכל פעם. במיוחד כשיש להם מכונות רציניות שיכולות להתמודד עם פנלים די גדולים, כך שכמה עשרות פנלים מספקים להם מאות מוצרים למלאי. בפוסטים די ישנים של SparkFun הם סיפרו שהם בחרו דגם מיוחד של מכונת השמה שתאפשר להם לעבור בין פרוייקטים כמה שיותר בקלות.
יצרנים גדולים יותר, כמו צוות Arduino, או Raspberry Pi Foundation, או יצרני טלפונים סלולריים למשל, הם בטוח מזמן כבר בשלב ייצור המוני עם כל המוצרים שלהם, אבל גם הם עברו דרך שלב אב-טיפוס וייצור סדרות קטנות.
באיזה שלב אני נמצא?
אני נמצא כרגע בשלב אב-טיפוס כי אני עדיין בשלב הוכחת יכולת של הרעיונות, אבל הכלים שרכשתי מכוונים גם לייצור סדרות קטנות. אם הייתי מתכנן להישאר רק בשלב הפיתוח של אב-טיפוס, הייתי בוחר כלים אחרים. אספר על זה בהמשך הפוסט.כמה מהטעויות שעשיתי היה ניסיון לדלג על שלב אב-טיפוס. כבר יש לי את המכונות פה, אני יודע שאצטרך בסופו של דבר פנלים בגודל מסויים… המעגלים די פשוטים… אז למה להזמין מעגלים קטנים לשלב אב-טיפוס? אלך ישירות על פנל שלם… טעות! לא משהו משמעותי, קצת עלויות משלוח, מעגלים ורכיבים שהיה אפשר לחסוך. אבל עדיין, לא כדאי לדלג על השלבים, אלא לקבל ביטחון ליציבות השלב לפני שעוברים לשלב הבא.
בהמשך אפרט על כל שלב ושלב בתהליך הייצור ואספר לכם מה עבד טוב, מה עבד פחות טוב ומה הייתי עושה אחרת. יהיו גם טיפים שימושיים לכל שלב. גם לאלה שבשלב אב-טיפוס וגם לאלה שיגיעו לשלב הסדרות הקטנות.
התהליכים בייצור המעגל הם: תכנון המעגלים, מריחת משחת בדיל, השמת רכיבים, הלחמה, תיקונים.
תכנון המעגל
בשלב אב-טיפוס רצוי להקטין את העלויות כי זה השלב שעושים בהם שינויים ותיקונים. כמות מעגלים מינימלית לטובת הבדיקות. גודל המעגל/פנל סביב 5-8 ס"מ מקסימום.בשלב הייצור, גודל הפנל צריך להיות מותאם ליכולת המכונות במיקום בו אתם מייצרים את המעגלים. יש מגבלות גודל למכונת מריחת בדיל, יש מגבלת גודל למכונת השמה ויש מגבלות גודל ומורכבות לתנור הלחמה. את גודל הפנלים צריך להתאים לכל המגבלות שיש בתהליכים.
עם מעגלים קטנים יחסית (כמו המייצב בגודל 14x12 מ"מ למשל) זה לא כל כך הגיוני לייצר מעגל בודד בגודל כל כך קטן, אבל לא צריך לרוץ ישר לפנל של 20x30 ס"מ. רצוי שבשלב אב-טיפוס יהיה מעגל בגודל סביב 5-8 ס"מ. זה יעזור עם מסכת בדיל (Stencil) שאספר עליה בסעיף הבא, ולרוב מפעלי ייצור PCB יציעו לכם מחירים מאוד אטרקטיביים למעגלים קטנים.
הנה עוד כמה דוגמאות של טעויות שהיו יכולות לחסוך לי קצת כסף:
עם המעגל ה"מסובך" יותר, כמו הבקר Plug-n-Play SAMD21 בהתחלה יצרתי PCB של מעגל אחד בלבד. גיליתי בעיות, תיקנתי ומרוב ההתלהבות את הגרסה השניה יצרתי כפנל של 4 כרטיסים, כמו שאפשר היה לראות בתמונה למעלה. אומנם בגרסה השניה לא טעיתי בעריכה פונקציונלית, אבל לא שמתי לב שנעלמו לי שני חורים כי לא סימנתי משהו בתוכנה. קיבלתי ביטחון יתר בתהליך והזמנתי 10 פנלים של הגרסה השניה במקום המינימום האפשרי של 5. כך שרובם ילכו לפח. תוך כדי היה אילוץ נוסף שדרש גרסה נוספת של המעגל, כך שבכל מקרה הייתי צריך לעבור לגרסה שלישית.
למודולים של חיבור מתח החלטתי לדלג על שלב אב-טיפוס ולייצר ישר פנל בתצורה הסופית. מה כבר יכול להשתבש במעגל קטן עם 2 מחברי SMD ומחבר אחד שצריך להלחים ידנית? אז זהו שיכול… התבלבלתי עם זה שהמחברים מולחמים משני צידי המעגל, אז החיווט לא היה נכון וקיצר את המעגל. המעגלים הלכו לפח. למזלי מסכת הבדיל (Stencil) לא השתנתה כי רק המוליכים על ה-PCB השתנו והרכיבים נשארו באותו המיקום.
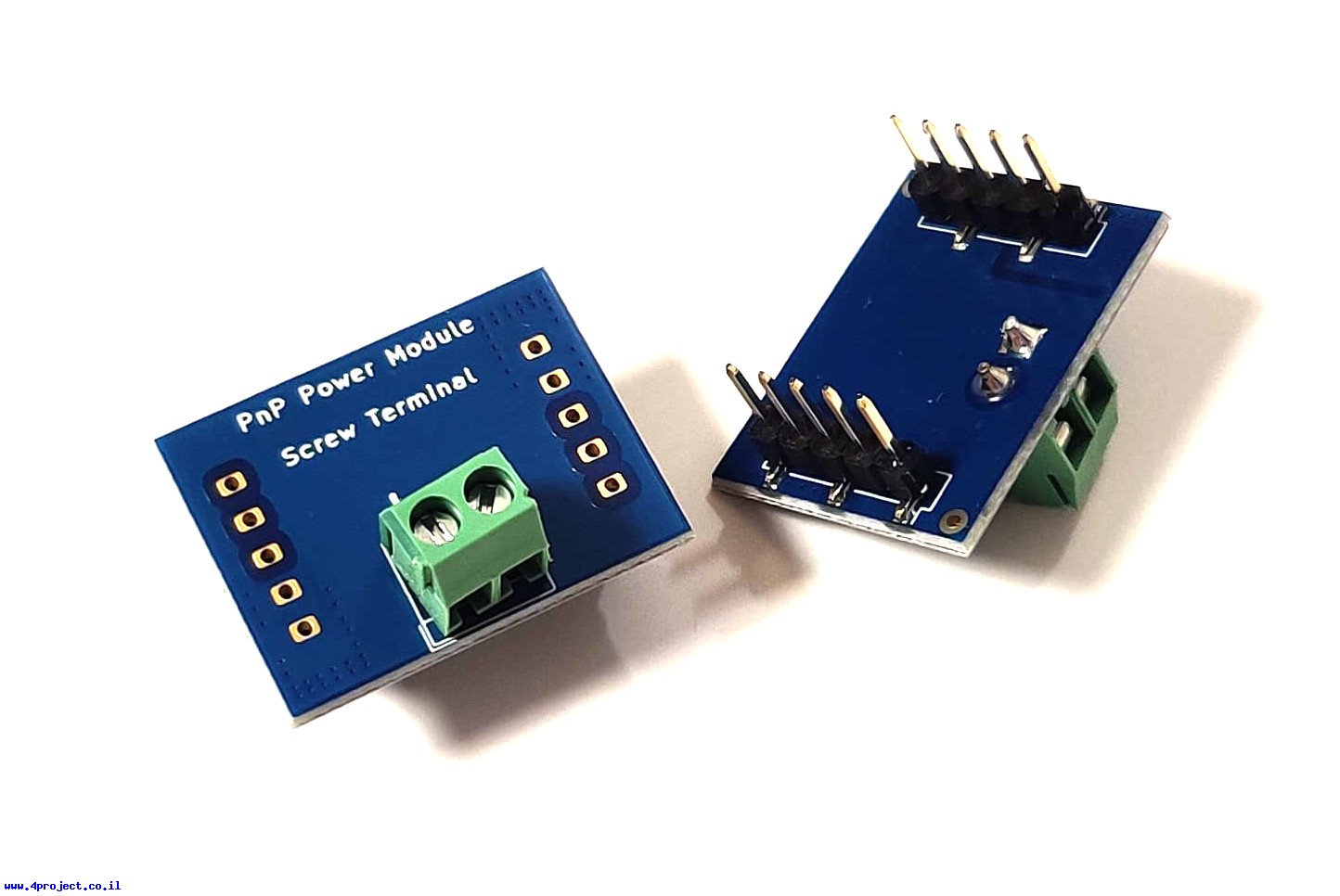
גם עם מתאם קטן בין חיבור Plug-n-Play למערכת QWIIC ניסיתי לדלג על שלב אב-טיפוס. טעות! במקרה הזה מיד הבנתי שהייתי צריך להוסיף נגדי pull-up לקווי הפסיקות, כך שכל המעגלים וגם ה-Stencil הלכו לפח. והמשלוח של ה-Stencil מקפיץ את המחיר פי 2-3 בהשוואה למשלוח של המעגלים בלבד.
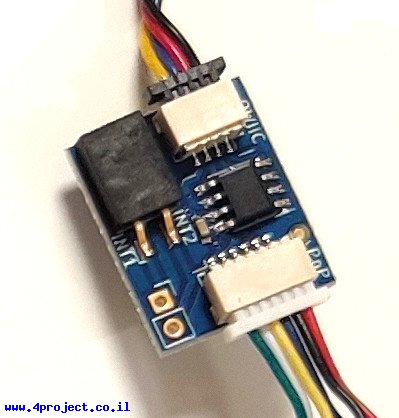
טיפים שימושיים:
תוסיפו שוליים סביב המעגל, מכל 4 הצדדים (צבע ירוק כהה בתמונה):
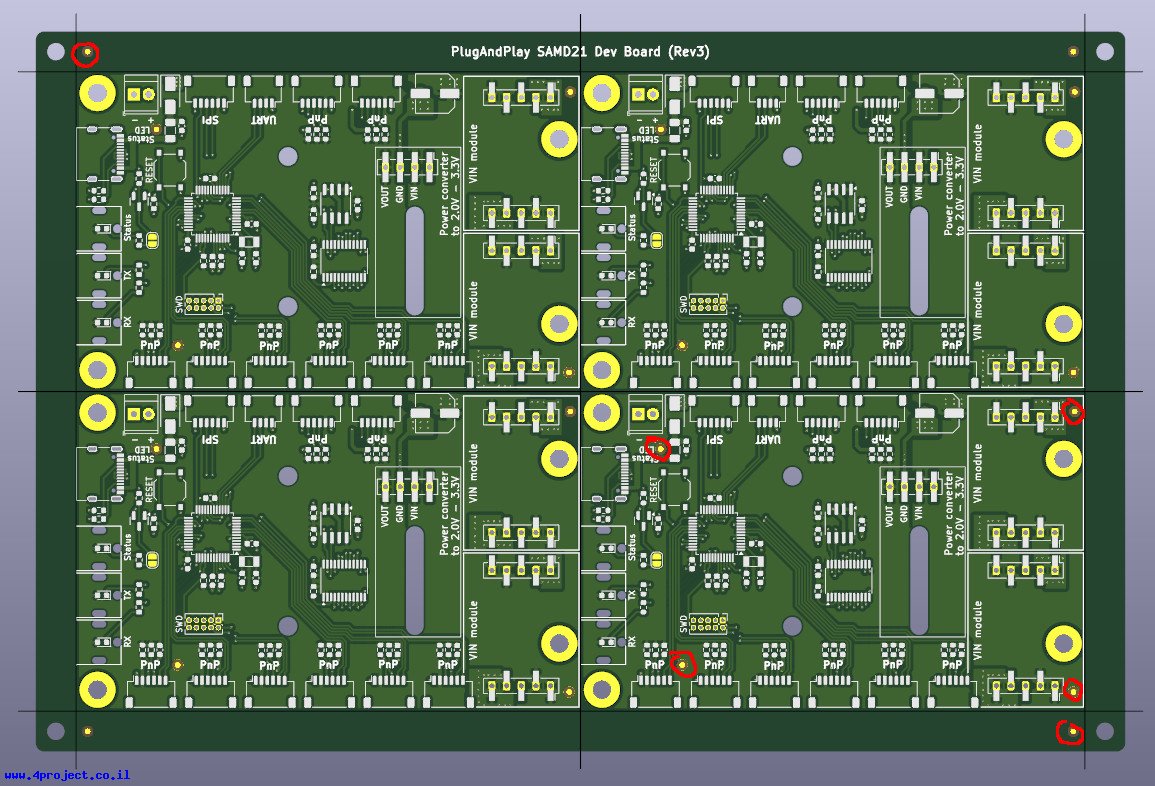
למה זה טוב? במהלך העבודה צריך להעביר את הכרטיס בידיים בין המכונות וקרה לי לא פעם שבטעות נגעתי ברכיבים שקרובים לקצה (ובמעגל הזה יש די הרבה כאלה), כך שהם זזו מהמקום לפני ההלחמה.
זה מוסיף קצת לגודל המעגל ולעלות שלו, אבל יחסוך זמן של תיקונים.
טיפ זה רלוונטי גם בשלבים הראשוניים כשאתם בטוחים שתרכיבו את הרכיבים ידנית, וגם כשהמעגלים יעברו השמת רכיבים במכונה, שם השוליים הם חובה משני צדדים של המעגל כדי שאפשר יהיה להרכיב את הפנל במכונה.
שוליים של 5 מ"מ בדרך כלל מספיקים. אני הוספתי של 7 מ"מ כדי שיהיה קצת יותר נוח לשבור אותם בסוף התהליך.
אני מעדיף להשתמש ב-V-cut לצורך הפרדת מעגלים בפנל, שזה חיתוך של כשליש מעומק ה-PCB משני הצדדים. אחרי זה פשוט שוברים את הלוח בעדינות לאורך החיתוך. יש כאלה שמעדיפים צורה של mouse bites להפרדת מעגלים. אני פחות חובב את שיטה הזו, אלא אם לא תהיה ברירה (מעגלים עגולים או בצורה מוזרה אחרת).
בתמונה למעלה תראו גם נקודות נחושת חשופה שסימנתי באדום במעגל הימני התחתון. נקודות אלה נקראות נקודות ייחוס (Fiducials), וכל מכונת השמה צריכה אותם כדי לחשב את המיקום היחסי של הרכיבים במעגל. זה משהו סטנדרטי ותוכלו למצוא אותם בכל תוכנת עריכה.
ב-KiCad למשל יש כמה גדלים של הסימונים האלה. למכונה שלי מצאתי ש-Fiducial בגודל 1 מ"מ של נחושת חשופה עם פתיחת ציפוי של 2 מ"מ עובדים בצורה יפה.
אם תסתכלו על המעגלים שיש לידכם, תמצאו את הסימונים האלה על כל מעגל.
בדרך כלל שני Fiducials במעגל יספיקו. במעגלים גדולים במיוחד רצוי להוסיף 4 כדי להוסיף נקודות ציון נוספות למכונה. על המעגל שבתמונה הוספתי 4 כדי לראות איך זה עובד עם המכונה שלי, אבל לא באמת צריך את כל ה-4.
בתמונה אפשר לראות שיש Fiducials גם על המסגרת החיצונית. מכונה שלי זקוקה להם כדי לזהות את המיקום הראשוני של הפנל.
לרוב אפשר להשתמש במיקומים של רכיבים שונים על המעגל במקום ה-Fiducial, אבל אם המעגל שלכם מתוכנן לעבור דרך מכונה כלשהי, רצוי להוסיף אותם מההתחלה.
יש גם 4 חורים בפינות הפנל. אלה דרושים כדי להרכיב את המעגל במכונת מריחת משחת בדיל. אתייחס לזה בסעיף הבא.
כמו שאתם יכולים לראות, תכנון המעגל קצת מושפע מהצרכים של המכונות. חשוב לברר את האילוצים של המפעל ולהוסיף את מה שדרוש בשלב התכנון של המעגל.
מריחת משחת בדיל
למשימה זו קניתי את המכשיר הזה של חברת NeoDen:
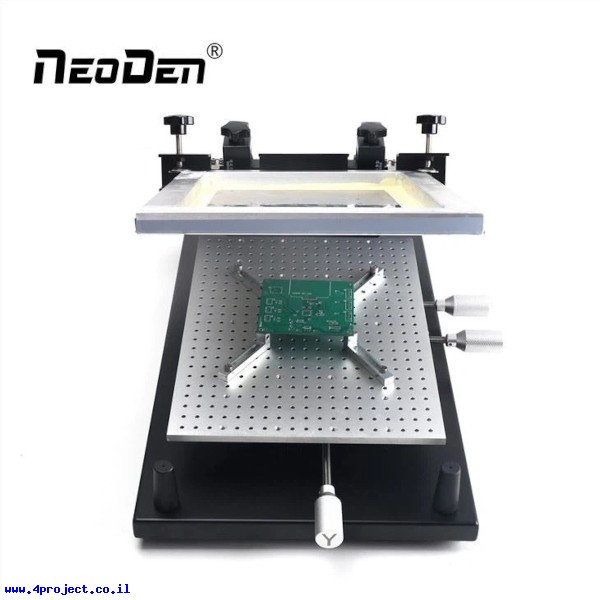
יש דגמים דומים באליאקספרס, עם זרוע ומשקולות מאחור, במקום הקפיצים שיש בדגם שקניתי. יש גם כאלה שהמשטח שלהם ללא חורים ויש מנגנון אחר לחיבור המעגל, מכני או מגנטי.
אני שלם לגמרי עם המכשיר הזה ומרוצה מהתוצאות. יש כאלה שיגידו שהוא מיותר ואפשר לקבל את אותן התוצאות גם בלי מכשיר מיוחד ועם זה אני פחות מסכים. זה יהיה מאוד תלוי בגודל המעגל וכמות שרוצים לייצר.
בסרטון זה בוב מ-SparkFun מדגים מריחת בדיל על מעגלים על השולחן, ללא מכשיר מיוחד:
אני מסכים עם זה שלא צריך שום מכשיר בשלב אב-טיפוס, אבל כן צריך מערכת יציבה כדי למרוח כמה מעגלים ברצף באותה האיכות.
הסיבה שבסעיף הקודם המלצתי על מעגלים/פנלים בגודל של 5-8 ס"מ לשלב אב-טיפוס היא כי בגודל הזה עדיין מאוד נוח לעשות את התהליך ללא צורך בציוד מיוחד. למרוח בדיל על פנל בגודל 20-30 ס"מ בצורה יציבה ועקבית יהיה יותר מאתגר.
כדי למרוח משחת בדיל על המעגל משתמשים במסכה (Stencil) עם חורים, דרכם הבדיל עובר על המעגל בדיוק במיקום הדרוש להלחמת הרכיבים. אפשר לייצר את המסכה בעובי בין 0.1 מ"מ ל-0.2 מ"מ, תלוי בכמות הבדיל שאתם רוצים שיהיה על המעגל. את המסכות (Stencils) בדרך כלל מזמינים מאותו המקום בו אתם מייצרים את המעגלים המודפסים (PCB).
מהניסויים שעשיתי ראיתי שמסכה בעובי של 0.1 מ"מ מצויינת לרכיבים קטנים (כמו הנגדים והקבלים) אבל לא משאירה מספיק בדיל למחברים גדולים, לכן כל המסכות שהזמנתי אחרי זה היו בעובי 0.12 מ"מ.
המסכות שמגיעות מסין עשויות מדף פלדה שנחתך לפי הקבצים שסיפקתם. ברירת המחדל היא שהמסכה מגיעה עם מסגרת אלומיניום, שמותחת את הדף מכל הכיוונים. זו הצורה שדרושה לטובת מכשיר למריחת משחת בדיל שיש לי וגם למכונות אחרות שעושות את זה (יש כאלה שהן חצי-אוטומטיות ויש מכונות אוטומטיות לגמרי שמטעינים להם מחסנית של מעגלים והיא עושה את הכל לבד).
בשלב אב-טיפוס אפשר להזמין את המסכות גם ללא המסגרת, מה שיחסוך לכם את עלויות המשלוח וקצת עלות המסכה עצמה. מפעל ממנו אני בדרך כלל מזמין את המעגלים מאפשר להזמין מסכה ללא מסגרת בגודל 10x15 ס"מ שתתאים לגודל המעגלים שהמלצתי עליו קודם (של 5-8 ס"מ).
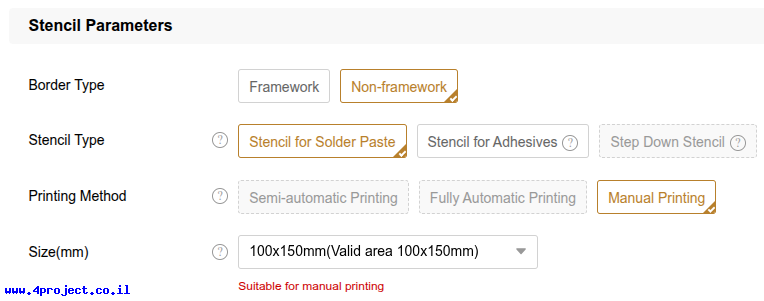
יש מקומות אחרים, כמו Pololu למשל, שמייצרים מסכות בדיל מדף פלסטיק שנחתך במכונת לייזר. מסכות כאלה פחות איכותיות, אבל יכולות להספיק לשלב אב-טיפוס אם אתם לא צריכים רזולוציה גבוהה מדי או כמות גדולה של שימושים. מסכת מתכת מאפשרת להגיע לרזולוציה טובה יותר ותחזיק מעמד הרבה יותר זמן. לא בדקתי לעומק, אבל כנראה שאין הגיון כלכלי להזמין אותן מ-Pololu. אם יש לכם גישה למכונת לייזר איכותית, אולי תוכלו לייצר מסכה במחיר סביר יותר.
טיפים שימושיים:
שוב אותו טיפ, אל תדלגו על שלב אב-טיפוס. השתמשו במסכה ללא מסגרת לשלב זה ולא תצטרכו מכשירים מיוחדים בשביל זה.
בדקו אם צריך חורים במיקום מיוחד למכשיר שיש לכם. במקרה שלי צריך 4 חורים כדי להחזיק את המעגל במקום. חברת EuroCircuits למשל מקדמת שיטה שהם קוראים לה eC-stencil-fix, שדורשת שני חורים במרחק ידוע במסגרת של המעגלים וגם של המסכה כדי שיתאימו אחד לשני על המשטח שהם מוכרים:
יש עוד פתרונות מעניינים בשוק שיעבדו מעולה עם מעגלים קטנים בשלב אב-טיפוס. מתקן כזה למשל יכול לספק יציבות אם אתם רוצים להרכיב את הרכיבים ידנית:
שימו לב שהוא משתמש במיקרוסקופ דיגיטלי כדי להדגים את הדיוק המתקן בסרטון. יש מכונות תעשייתיות שמגיעות עם 2 מצלמות ו-2 מסכים, כך שאפשר לראות שתי נקודות בו זמנית ולפי זה לכייל את מיקום המסכה מעל המעגל בצורה מדוייקת. כיול זה אחד הדברים הפחות נחמדים עם המכונות הידניות כמו שיש לי, ובגלל זה אם רוצים לייצר מעגל אחד או שניים, אנשים מעדיפים להדביק את הכל על השולחן, כי סידור הפינים שמחזיקים את המעגל על המכונה + כיול יכולים לקחת יותר זמן בהשוואה לשיטה הפשוטה יותר על השולחן.
היו לי מחשבות לקנות מיקרוסקופ דיגיטלית על זרוע בסגנון הזה כדי שיעזור לי בשלב הכיולים:
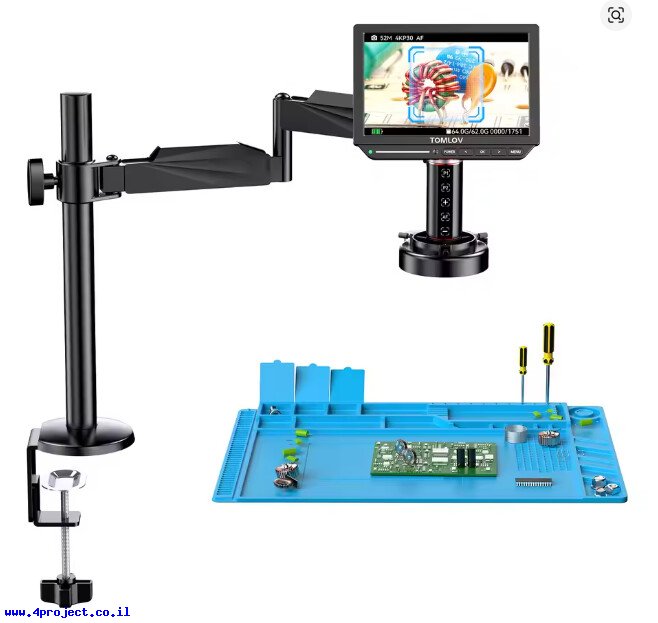
אומנם לא 2 מצלמות בו זמנית, אבל גם זה יעזור כי המכשיר שלי נמצא מתחת למדף ולא תמיד נוח לי להכניס את הראש מתחת כדי להסתכל בדיוק מלמעלה ולוודא שהכיול מדוייק. גם ההשתקפות מהמנורה שמעל המכשיר לא עוזרת.
מיקרוסקופ כזה הוא גם כלי מאוד שימושי לתיקונים, במיוחד עם רכיבים קטנים.
השמת רכיבים
גם על הרכישה של מכונת השמה מדגם שבחרתי בסופו של דבר אני לא מצטער. עושה את מה שציפיתי שיעשה ועושה בצורה טובה.לא חסרות בעיות גם עם מכונה זו, אבל הבעיות בעיקר מאופן השימוש שלי ולא בגלל שהמכונה לא טובה.
למשל, בגלל שכרגע אני לא מייצר כמויות גדולות של הכרטיסים, אני גם מזמין כמויות קטנות של רכיבים שהם יקרים יחסית ואין הגיון להזמין אלפים בלי שאני יודע שאצטרך אותם. נגדים וקבלים הזמנתי גלילים שלמים של 5000 יחידות כי כל הגליל עולה 3-$5. אם כבר אני משלם על המשלוח, אז חבל לא לקחת גליל שלם. אבל לדוגמה, את הגבישים (crystals), שצריך רק יחידה אחת על כל כרטיס של מיקרובקר, הזמנתי רק סרט חתוך של 150 יחידות. או אפילו מחברי JST-SH שצריך על כל כרטיס מסדרת ה-Plug-n-Play הזמנתי גם בחתיכות של 100-200 כל פעם (לא יודע למה).
גיליתי שהמחסניות של המכונה לא כל כך אוהבות סרטים קצרים. הכוח איתו הסרט מקודם ע"י המחסנית גורם לרכיבים לקפוץ, להסתובב במקום ולפעמים גם לעוף החוצה. והתופעה מחמירה לקראת סוף הסרט במחסנית. כנראה שכשיש גליל שלם, אז הזנב שנשאר על הגליל נותן קונטרה למשיכה של הסרט בזמן שהרכיבים מקודמים וקצת מעדן את התנועה.
בפורומים בהם אני מסתובב אנשים טוענים שאפשר לשים משהו מתחת לסרט בתוך המחסנית (יש מקום ריק כדי לאפשר רכיבים בגובה שונה להיות מותקנים באותה המחסנית), וכך לרכך את התנועה. עוד לא ניסיתי את זה, אבל זה בהחלט אחד הכיוונים לפתרון.
טעינת המחסנית עם סרט חתוך ולא גליל שלם גם לוקחת קצת זמן. צריך להדביק תוספות כדי שהמחסנית תוכל למשוך את הסרט עם הרכיבים וגם לקלף את כיסוי הניילון שיש מעל הרכיבים. הכל אפשרי, אבל לוקח זמן.
אני מתכנן להוסיף בסיס מתכתי למכונה שלי, במקום הפנוי שנשאר אחרי שמרכיבים מעגל PCB, ולהדפיס מחזיקי סרט עם מגנטים בבסיס, כך שאפשר יהיה להצמיד אותם ללוח המתכת ולהגדיר אותם כמערך זמני של רכיבים במכונה. רכיבים שלא בשימוש נפוץ במעגלים שאני מתכנן, כמו הגביש, דיודה או קבל אלקטרוליטי, שצריכים רק יחידה של כל אחד מהם במעגל של בקר ה-SAMD21, יכולים להיות במחסניות הזמניות האלה. יש לי רק 4 כרטיסים של הבקר בפנל, כך שגם אם אייצר 10 פנלים, אצטרך לקדם את הרכיבים במחסנית הזו רק פעם-פעמיים.
זה גם יפנה לי כמה מיקומים של מחסניות, שגם ככה אין יותר מדי במכונה שיש לי (40 מיקומים של מחסניות סרט של 8 מ"מ), זה יחסוך לי קצת זמן של החלפת מחסניות בין הכרטיסים השונים. כמות המיקומים שיש במכונה מספיקה בקושי לייצור מעגל במורכבות כמו הבקר SAMD21.
כל התוכנות האלה דורשות עוד כלי שעדיין אין לי - מדפסת תלת מימד. שאני בהחלט שוקל לקנות בקרוב.
2 ראשים שיש למכונה זו מגבלה שהיתה ידועה לי גם קודם. במעגלים עם רכיבים בגדלים שונים צריך פיות (nozzles) לכל גודל של רכיב ושתי פיות לא מספיקות להכל. את הכרטיס של בקר SAMD21 אני מרכיב בשני מחזורים, אחד עם רכיבים קטנים והשני לגדולים. זה היה ה-trade-off בין הזמן שאצטרך להשקיע במהלך ההרכבה לבין עלות המכונה ומקום שאין לי למכונה גדולה יותר. אם אגיע לשלב שאצטרך ייצור גדול ומהיר יותר, צריך מכונה עם מינימום 4 ראשים. אחת המחשבות ברכישה של המכונה שיש לי היתה שאפשר יהיה להשתמש במחסניות הרכיבים עם מכונה גדולה יותר כשיגיע הזמן, וזה יחסוך לי חלק גדול במעבר.
ניסיתי כל מני משחקים עם התוכנה כדי שתרכיב את כל הרכיבים הקטנים, תעצור כדי שאוכל להחליף את הפיות, ואז תמשיך עם הרכיבים הגדולים. אפשרות זו לא קיימת בתוכנה כברירת מחדל, אבל אפשר לשנות הרבה דברים ידנית ולרמות אותה כדי שהיא תנסה להרכיב רכיב שלא קיים כדי שתיעצר. לא יודע עד כמה זה מועיל. אם צריך להרכיב כמות, יהיה יותר פשוט להרכיב 10 פנלים עם רכיבים קטנים, אחרי זה סיבוב נוסף של אותם הפנלים לרכיבים גדולים. כנראה שזה יהיה מהיר ובטוח יותר מאשר להחליף פיות לכל מעגל.
התוכנה של המכונה יחסית בסדר בהשוואה למה שאני רואה אצל יצרנים סיניים אחרים. לא הכל מושלם, אבל מתרגלים להגיון שלהם די מהר ומעגל שני ושלישי לקח לי הרבה פחות זמן לתכנות המכונה.
השבוע שברתי ראש אחד במכונה בגלל שבטעות הגדרתי רכיב בגובה 3 מ"מ (socket) במקום רכיב של 10 מ"מ (header), כך שהמכונה דפקה את הרכיב על המעגל בכל הכוח והתעקם ציר המנוע שמסובב את הרכיבים. פניתי לנציג היצרן והם כבר שולחים לי את הרכיבים להחלפה. עלות של $98 לשני סטים, אחד להחליף את מה שהתקלקל והשני שיהיה ספייר. מתוך הסכום הזה $50 זה המשלוח.
זה היופי במכונה סינית. הייתי יכול להזמין את המנועים האלה גם מאליאקספרס אם הייתי צריך. במקרה הזה רציתי לפתח קצת יותר קשרים עם היצרן כי הנציג שלהם מאוד ידידותי ואוהב לעזור.
עם מכונות אירופאיות או יפניות היה צריך כנראה להטיס טכנאי מהקצה השני של העולם והיה צריך משכנתא רק בשביל זה. כל זה במקרה שהמכונה לא ישנה מדי, שמשלמים דמי אחזקה חודשיים (של אלפי דולרים) והם עדיין מספקים לה שירות.
טיפים שימושיים:
מכיוון שיש לי כבר את המכונה, אז אני משתמש בה גם בשלב אב-טיפוס. אבל אם אתם מתכוונים לייצר מעגלים בעצמכם, אין בעיה להרכיב את הרכיבים ידנית. זה פשוט לוקח יותר זמן. אל תשתמשו ברכיבים קטנים מדי. רכיבים בגודל 0805 אפשר להרכיב ידנית די בקלות בלי שום מכשור. תכננו את המעגל בהתאם ליכולת שלכם. אני הלכתי על רכיבי 0603 כי ידעתי שאשתמש במכונה כדי להרכיב אותם.
רכיבים הקטנים אגב הם לא הבעיה, גם אם תרכיבו אותם קצת בזווית או לא בדיוק במיקום הנכון, הבדיל ימשוך אותם למקום במהלך ההלחמה. רכיבים גדולים יותר, עם הרבה רגליים צפופות, כמו מיקרובקרים, הם הבעייתיים יותר ודורשים דיוק בהשמה שלהם על המעגל. צריך יד יציבה (בסיס כף היד נשען על השולחן ולא באוויר) ועם קצת ניסיון ואפשר להגיע לתוצאות טובות.
יש בשוק גם מכשירים להרכבה ידנית של רכיבי SMT, שנראים כמו צירים X/Y עם משטח שמחליק עליהם, כך שאפשר להשעין את היד על המשטח תוך כדי תנועה. יש גם מכשיר שיכול להרים את הרכיבים עם ואקום במקום פינצטה. לא השתמשתי בכאלה אף פעם. פחות ממליץ עליהם, אלא אם אתם מתכננים להרכיב הרבה מעגלים ידנית (בתור ספק הרכבות לאחרים).
הלחמה
הגענו לשלב שאני לא מרוצה מהקניה שלי.להזכיר, קניתי תנור מגירה מדגם T937, שאמור להיות מסוגל לבצע הלחמות של בדיל נטול עופרת:
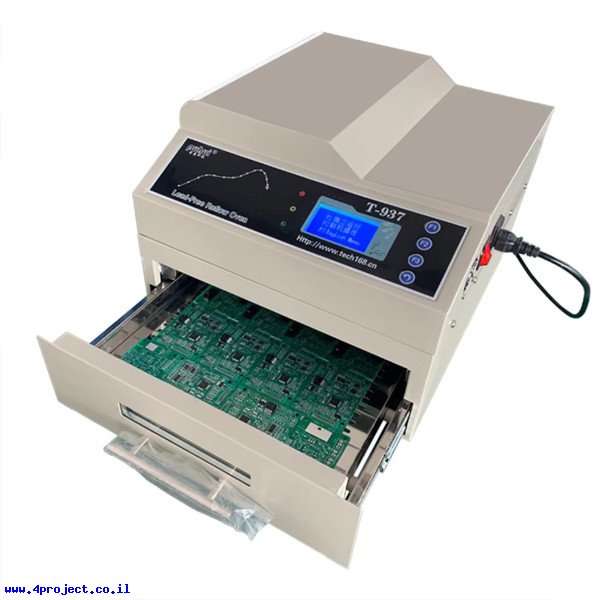
במפרט של המכונה רשום שאפשר להלחים בה מעגלים עם בדיל נטול עופרת עד לגודל של 260x260 מ"מ. בפועל, אני מתקשה לקבל הלחמות טובות בכל המעגל, גם אם הוא בגודל קטן מ-150x200 מ"מ. ברור שמה שרשום זה במילימטרים סיניים, אבל עדיין, לא ציפיתי שזה יהיה כל כך גרוע.
היה ידוע לי שלתנור מגירה יש די הרבה בעיות, בגלל זה קניתי דגם קצת יותר משופר מהפשוטים ביותר, אבל עדיין אין לו מספיק כוח למשימה.
אחת הבעיות עם תנורים כאלה הם נקודות חמות. בתנור יש 4 מנורות אינפרה אדומות (IR) שמייצרות את החום הדרוש להלחמה. בגלל שהמעגל יושב סטטי במגש, אז הנקודות שבדיוק מתחת למנורה מקבלות יותר קרינה מהנקודות שבין שתי המנורות. יש גם הבדלים בין המרכז של המגירה לצדדים שלה. ל-T937 יש מאוורר פנימי שמערבל את האוויר במגירה, מה שאמור לפזר את החום בצורה שוויונית יותר על כל שטח המעגל.
בעיה נוספת היא שבגלל שהחימום מתבסס על אור אינפרה אדום שמגיע מהמנורות, רכיבים גבוהים יכולים להסתיר חלק מהאור הזה ולגרום לצל על נקודות מסויימות, שמקבלות פחות קרינה ולא מגיעות לטמפרטורה הרצויה.
ההמלצה של היצרן היא להגדיל את הטמפרטורה עוד קצת, אבל אז המחברים שעל המעגל נשרפים ומתחילים להתעוות. ולמה שאני רוצה לעשות יש מחברים כמעט על כל מעגל.
בקיצור, כל מה הזהירו ממנו קרה.
אסביר קצת על תהליך ההלחמה למי שרוצה להתעמק.
ה"סטנדרט" בתעשיה הוא להשתמש בבדיל נטול עופרת, המכונה בשם SAC305 בגלל הרכב הכימי שלו: Sn96.5/Ag3.0/Cu0.5. נקודת ההתכה של בדיל כזה היא באיזור ה-220 מעלות. כל יצרן של הבדיל מספק פרופיל טמפרטורות שהם ממליצים לטובת הלחמה תקינה. זה הגרף מהמפרט של בדיל TS391SNL250 של חברת
Chip Quik שיש לי:
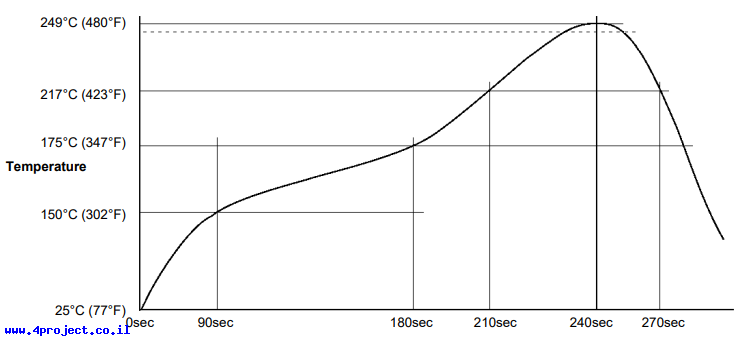
זו לא סתם המלצה שרירותית, לכל איזור בגרף יש משמעות לזמן ולטמפרטורה.
ב-90 השניות הראשונות מחממים את המעגל ל-150 מעלות כהכנה לשלב בו ה-Flux מתחיל לעבוד. בין 90 ל-180 שניות יש עליה מתונה בטמפרטורה, שהיא בעיקר לתת זמן ל-Flux להרטיב את המגעים. בין 180 ל-210 שניות מעלים את הטמפרטורה לרמת ההתכה של הבדיל ועידוי ה-Flux. בין 210 ל-240 שניות הבדיל אמור להפוך לנוזל ולזרום למיקום ההלחמה על המעגל ולהתחבר לרכיבים. אחרי זה מגיע שלב הקירור, שרצוי שהטמפרטורה בשלב זה תרד מתחת לטמפרטורת ההתכה של הבדיל תוך 30 שניות הבאות.
אין יותר מדי מקום למשחק עם נתונים אתה. עליה חדה מדי של הטמפרטורה יכולה לגרום לרתיחה של ה-Flux, שיפזר את כדוריות הבדיל לכל עבר, תעוות את המעגל, או אפילו תגרום לסדקים בו. להאריך את הזמן חימום מ-150 ל-220 מעלות יגרום ל-Flux להתייבש לפני ההלחמה. להאריך את הזמן של העליה הגדולה של הטמפרטורה תחשוף את הרכיבים לטמפרטורה גבוהה למשך זמן ארוך מדי (למחברים למשל זה בדרך כלל עד 10 שניות לטמפרטורה מעל 240 מעלות).
נקודה חשובה שצריך להבין עם הלחמות, זה שאם הבדיל נמס ב-220 מעלות, זה לא מספיק שתקרינו על נקודת ההלחמה חום של 250 מעלות. כל איזור ההלחמה צריך להיות מעל 220 מעלות! אם המעגל עצמו לא מחומם מספיק, אז הוא מתפקד כמפזר חום וגונב את החום מהבדיל. רכיב גדול שלא התחמם, גם הוא גונב את החום. לדוגמה, מחבר USB-C שעשוי ממתכת מבריקה לא מתחמם כמו שבב שחור מכיוון שהוא מחזיר את האור של מנורת IR, כך שלוקח לו יותר זמן להתחמם בתנור מגירה כמו שיש לי.
פניתי לתמיכה של ChipQuick כדי לנסות למצוא פתרון. רוצה לשבח אותם על הנכונות לעזור ולהסביר על התהליכים. המליצו להגדיל את הזמן הראשוני לפני שמגיעים ל-150 מעלות בתקווה שזה יעזור לחמם את הכל קצת יותר טוב. 150 מעלות זו הטמפרטורה שבה ה-Flux מתחיל לפעול וכל מה שקורה לפני כן לא משפיע על הבדיל. זה עזר קצת. המליצו גם לנסות להגדיל קצת את זמן העליה לטמפרטורה המקסימלית. גם זה עזר קצת, אבל מתחיל לשרוף את הפלסטיק של כפתורים על אחד המעגלים. ועדיין, יש מקומות במעגל שלא הולחמו כמו שצריך, כך ששינויים אלה לא פתרו לגמרי את הבעיה.
מה אפשר לעשות? אפשר לעבור לבדיל נטול עופרת שמבוסס על ביסמוט (Sn42/Bi57.6/Ag0.4) וזקוק לטמפרטורות דומות לבדיל עם עופרת - רק 165 מעלות. לבדיל זה יש חסרונות משלו, כך שאני לא רוצה ללכת לכיוון הזה.
נראה שאין מנוס, ואצטרך לרכוש תנור הלחמה קצת יותר תעשייתי. מקווה שאותו קו המחשבה כמו עם מכונת ההשמה יעבוד. צריך למצוא מכונה תעשייתית מוקטנת ולא מכונת prototyping מוגדלת…
בתחום זה אין יותר מדי אפשרויות. מכונה תעשייתית רצינית זו מפלצת באורך של לפחות 2 מטר ושוקלת באיזור ה-300 קילו:
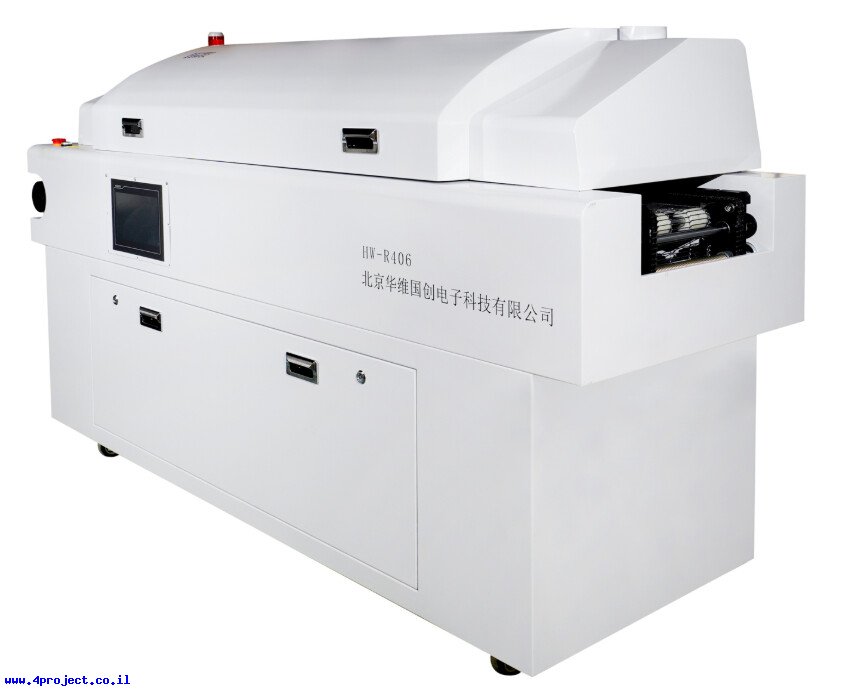
אם בתנור מגירה המעגל יושב במקום וגופי החימום מנסים לייצר את פרופיל הטמפרטורות שקבענו, במכונות תעשייתיות יש רשת שמסיעה את המעגל לאורך כמה איזורי חימום, כאשר כל איזור מנסה לשמור על הטמפרטורה שהגדירו. למכונות טובות יותר יש גופי חימום גם מעל המעגל וגם מתחת. גופי חימום לא מחממים את המעגל ישירות, אלא מחממים את האוויר סביבם, שנדחף על המעגל בעזרת מאוורר של אותו האיזור. באיזורי חימום התחתונים בדרך כלל אין מאווררים כי החום בכל מקרה עולה למעלה.
כמות גדולה יותר של האיזורים מאפשרת דיוק רב יותר בפרופיל הטמפרטורה. מכונה ארוכה יותר היא יותר סלחנית לאי דיוקים כי המעגל עובר מהר יותר דרך נקודות שונות בתנור ולא מתעכב באיזורים בעיתיים אם יש כאלה. למכונה שבתמונה למעלה יש 4 איזורים עליוניים ו-2 תחתונים. יש מכונות גם עם 6 ויותר איזורים מכל צד.
ברגע של חולשה כמעט והזמנתי תנור קטן יחסית מהיצרן של מכונת ההשמה שיש לי, אבל למזלי שמתי לב שבמסמך שהוא שלח לי רשום שלתנור שהוא הציע יש 3 איזורים עליוניים ואין חימום מתחת למעגל. למרות שבאתר האינטרנט היה רשום שזה דגם עם 3+3 איזורים.
למה צריך חימום תחתון אם הבדיל הוא בצדו העליון של המעגל? זו נקודה חשובה שהסברתי קודם: המעגל כולו צריך להתחמם לטמפרטורת ההלחמה, ולא רק הבדיל! במקום להפציץ את המעגל והרכיבים רק מלמעלה ב-300 מעלות כדי שהכל יתחמם ל-250 מעלות, אפשר לעזור גם מלמטה עם חימום של כ-200 מעלות ומלמעלה רק עם 260. חימום משני הצדדים בריא יותר ל-PCB עצמו וימנע עיוות.
נושא אחר שחשוב בתנורים כאלה הוא עוצמת גופי החימום עצמם. איזורי החימום צריכים לשמור על הטמפרטורה בצורה טובה, אחרת מעגלים שונים, עם רכיבים שונים יתנהגו בצורה שונה כשהם עוברים דרך התנור. זה גם קובע את גודל המעגל וקצב הכנסת המעגלים לתנור. מעגל על יותר שכבות (יותר נחושת), או עם רכיבים גדולים במיוחד (FPGA ענקי) יספוג יותר חום מאשר מעגל קטן של 2 שכבות. התנור צריך יהיה להגביר את החימום כדי להתאושש לחזור לטמפרטורות שנקבעו לו. זו הסיבה שתנורים תעשייתיים זוללים לא מעט חשמל וזקוקים לחיבור תלת-פאזי כדי שאפשר יהיה לספק להם את כל הזרם.
אז מה האפשרויות שיש לי? אני בטוח שמפלצת של 2 מטר תעשה את העבודה בצורה מושלמת, אבל זה הרבה מעבר למה שאני צריך. תנורים כאלה מותקנים בפסי ייצור שמטפלים בייצור המוני. להשתמש בהם לטובת אב-טיפוס וייצור סדרות קטנות הוא בזבוז של משאבים. לוקח להם 30 דקות להתחמם לטמפרטורות הרצויות. כל זה רק כדי להעביר בהם פנל אחד או שתיים?
חוץ מבזבוז החשמל, פשוט אין לי מקום למכונה שתתפוס לי 2 מטר של רצפה. גם לא בטוח שאפשר להעביר כזו דרך הדלתות של המשרד.
לאותו היצרן (Puhui) של תנור T937 יש כמה דגמים קטנים יותר, שמוגדרים כ"שולחניים". כולם מבוססים על מנורות IR לחימום, אבל המכונה עצמה בנויה בתצורה של מכונה תעשייתית עם מסוע. אנשים שומעים מנורות IR וישר מעלים חששות בגלל כל הבעיות איתן בתנורי מגירה, אבל השימוש בהם במכונות האלה שונה. אנשים שיש להם תנור מדגם T960 מרוצים מהתוצאות. זהו תנור באורך של כ-1.5 מטר עם 3 איזורי חימום עליונים ו-2 תחתונים. עם 96 ס"מ אורך כולל של איזור החימום. המכונה עדיין זקוקה ל-3 פאזות ודי גדולה, כך שהיא צריכה שולחן משלה, מה שאומר שהיא תתפוס מקום רצפה שאין לי.
יש בשוק שני תנורים עוד יותר קטנים בשוק. שניהם זקוקים רק לפאזה אחת של חשמל, שניהם באורך של מטר אחד ושניהם מגיעים בקונפיגורציה של 3 איזורים מעל ו-3 מתחת למעגל.
תנור אחד הוא דגם IN6 של NeoDen:
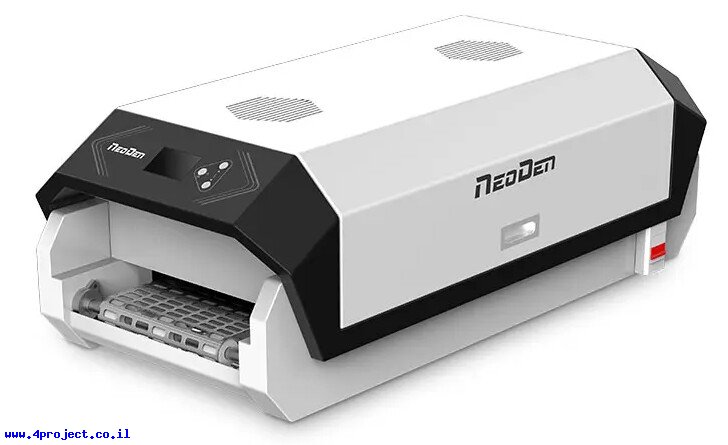
על ההגיון של NeoDen כתבתי בפוסט הקודם, כך שזה כבר מוריד מהחשק לקנות מהם משהו. ויש גם לא מעט ביקורות לא טובות על המכונה הזו. יש להם מפיץ בארה"ב והם מכרו שם לא מעט מכונות כאלה, כך שיש הרבה אנשים בפורומים שיכולים לספר עליה. רוב הבעיות הן סביב גופי החימום המיוחדים שלהם, שנשרפים בקלות, במיוחד בהלחמות עם בדיל נטול עופרת שדורש טמפרטורות גבוהות. היו גם דיווחים על זה שהמכשיר מקפיץ את ממסר הפחת בחורף כשיש לחות. וכולם אומרים שהמכונה חלשה מדי, צריך לחכות לפעמים 20-30 שניות בין מעגל אחד לשני. לפי המפרט היא צורכת 1800W מקסימום (בחימום ראשוני) ו-700W תוך כדי עבודה. לפי היצרן, למכונה זו לוקח 25-30 דקות להתחמם כדי שאפשר יהיה להכניס מעגל ראשון…
נראה שהשקיעו בעיצוב של המוצר, אבל האיכות עדיין לא משהו. לא רוצה להכליל יותר מדי, אבל בכללי, התובנות שלי לגבי היצרנים הסיניים: אם המוצר יפה מדי, עם מסך LCD Touch או שיש תוכנה שמעורבת בהפעלה של המכשיר - בדקו ב-7 עיניים. כל אלה סימנים שהמוצרים מכוונים לשוק המערבי, זה לא אומר שהם איכותיים יותר. לשוק המקומי הם מייצרים מכשירים כמה שיותר Low-Tech, עם כמה כפתורי הפעלה כדי שכל אדם מהכפר יוכל להפעיל את המכונה בלי להסתבך. ובנושא התוכנה הם לא כל כך מפותחים כמו המערב.
מכונה אחרת היא שוב של Puhui מדגם T961, שגם היא מבוססת על מנורות IR, פשוט קטנים יותר:
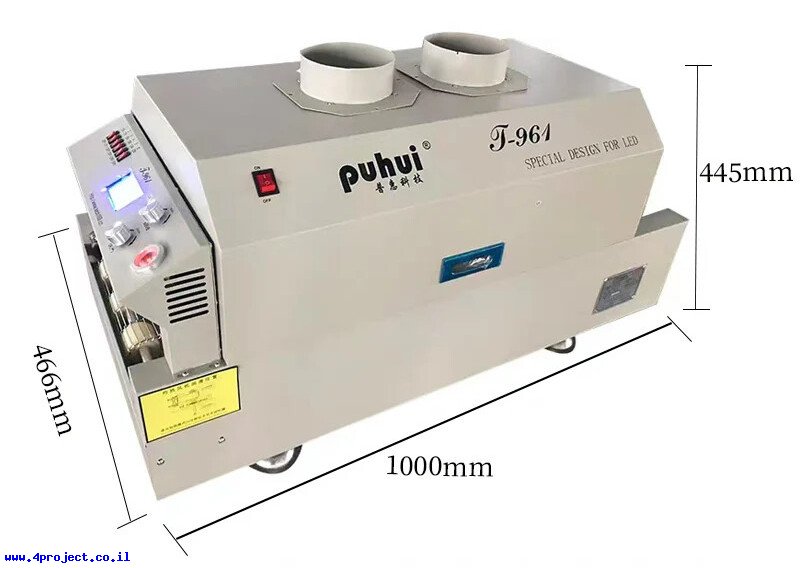
כאמור, למכונה זו יש 3 איזורי חימום מעל ו-3 מתחת למעגל. 730 מ"מ אורך כולל של איזור החימום.
המכונה שוקלת 70 קילו ונראה שאוכל למקם אותה על הדלפק מעל השולחן, במקום תנור המגירה. לא יודע לגבי נוחות העבודה בגובה כזה, אבל נראה לי שאפשר להסתדר.
המכונה צורכת 3500W מקסימום (לחימום ראשוני) ו-1900W תוך כדי עבודה. לפי היצרן לוקח לה כ-7 דקות להתחמם למעגל ראשון. גם אם אלה 7 דקות סיניות ובפועל לוקח פי 2 זמן להתחמם, זה עדיין יהיה כנראה מהר יותר מה-IN6. גם בהספקים אפשר לראות שלמכונה כנראה יש יותר כוח. בסופו של דבר כל ההספק שהיא זוללת מתורגם לחום שנזרק על המעגל. אם IN6 מצליח להלחים מעגל עם צריכה של מקסימום 1800W, אז אני רוצה להאמין ש-3500W יצליחו לעשות את זה טוב יותר.
הרצון למקם את התנור במקום ה-T937 שיש לי נובע גם מזה שהוסיפתי במיקום הזה קו חשמל של 16A יעודי לטובת התנור, כך שהייתי שמח לא לשלם על התקנת קווים נוספים.
כמובן שמכונות כאלה קטנות וחלשות יותר מהתעשיתיות. ל-T961 אפשר להכניס מעגל ברוחב מקסימלי של 230 מ"מ. לא חושב שזו בעיה גדולה בשבילי. בינתיים המעגלים שתכננתי כוונו לרוחב של 15 ס"מ ופחות. אם באמת אפשר יהיה להלחים מעגלים ברוחב של 20 ס"מ, אז זה יהיה בכלל מעבר לציפיות שלי.
בינתיים נראה שאני קונה את המכונה הזו. מחכה לכמה פרטים מהנציגה שלהם כדי להבין שאני לא מפספס משהו. מקווה שזו לא תהיה עוד נפילה כמו עם ה-T937 שיש לי. אנשים מרוצים ממכונה קצת יותר גדולה, ה-T960, כך שהטכנולוגיה עושה את העבודה שלה והיצרן כנראה יודע מה הוא עושה (רק תנורי הלחמה וציוד בתחום זה). ה-IN6 מצליחה לבצע הלחמות, כך שהאורך הקצר של המכונות האלה כנראה עדיין מאפשר להגיע למה שפרופיל הטמפרטורות של יצרני הבדיל דורש. ללא ספק צריך יהיה לשחק עם הכיולים כדי להגיע להגדרות הנכונות, ובשביל זה כבר הזמנתי לוגר (Logger) של טמפרטורה, שיכול להקליט את המדידות ואחרי זה אפשר יהיה לראות אותם כגרף על המסך. זה עוזר להבין מה הלוח שעובר במכונה "מרגיש" באמת.
טיפים שימושיים:
כמו שכבר הבנתם, אני לא ממליץ על תנור מגירה לייצור של סדרות קטנות. גם לא לשלב של אב-טיפוס. לסדרות קטנות התנורים האלה לא מצליחים להתמודד עם גודל מעגל קטן יחסית. ולאב-טיפוס יש פתרונות זולים יותר, קטנים ופשוטים יותר. רוב הסיכויים שהתנור שיש לי יעשה עבודה טובה עם בדיל שדורש טמפרטורה נמוכה, אבל זה לא הכיוון שלי כרגע.
אם אתם מייצרים מעגלים כתחביב, לשימוש עצמי, בכמות קטנה, כנראה ששימוש בבדיל שכולל עופרת יקל עליכם מאוד. בדיל נטול עופרת שמבוסס על ביסמוט לא זקוק לטמפרטורות גבוהות כמו בדיל נטול הסטנדרטי SAC305, גם הוא יכול להיות אופציה שצריך לבדוק. אנשים התלוננו על כך שבדיל שמבוסס על ביסמוט שברירי מדי, מה שבעייתי עם רכיבים מכניים, כמו מפסקים וכפתורים. אבל שמעתי גם שבשנים האחרונות איכות הבדיל מסוג זה השתפרה והם לא רואים שום בעיה בשימוש.
אם אתם מתכננים להגיע לייצור סדרות קטנות, הייתי ממליץ להשתמש בבדיל נטול עופרת מההתחלה, גם בשלב אב-טיפוס כדי שתהיה עקביות בתהליכים ולא יהיו הפתעות.
אז איך מלחימים אם תנור המגירה לא כזה מומלץ? יש כאלה שממליצים לטובת אב-טיפוס להפוך טוסטר אובן לתנור בעזרת בקר מיוחד, שנמכר ברשת במיוחד למטרה זו. רק שהתנור עצמו והבקר יכולים להגיע למאות דולרים, כך שאני לא ממליץ על זה.
יש אנשים שמצליחים להלחים מעגלים על מחבט חשמלי עם חול (כדי שיהיה יותר מגע בין משטח המתחמם למעגל). מפעילים את המחבט על 300 מעלות, שמים את המעגל על החול, מחכים שהבדיל הופך לנוזלי ומוצאים את המעגל עם פלייר. יכול לעבוד לכמות קטנה של מעגלים קטנים.
אפשרות יותר "מודרנית" היא להשתמש באותם הכלים בהם משתמשים לתיקון מעגלים - פלטת חימום ותחנת אוויר חם, עליהם אדבר ב סעיף הבא של הפוסט.
וכמובן לא לשכוח את הכלי הסטנדרטי שצריך להיות לכל אחד שמתעסק עם מעגלים - המלחם. אם אתם לא יורדים מגודל הרכיב 0805, יהיה לא קשה במיוחד להלחים את כל המעגל ידנית. אפשר להלחים גם את המיקרובקרים עם הרבה רגליים, אפילו בלי מסכת בדיל (Stencil) וגם בלי משחת בדיל. פשוט מתיכים את הבדיל הרגיל על כל הרגליים כדי שיהיה חיבור בין הרכיב למעגל. את הבדיל העודף מורידים אחרי זה עם מסיר בדיל ובודקים היטב שאין קצרים.
הנה סרטון שמדגים הלחמת רכיבי SMT עם מלחם רגיל:
תיקונים
אם לא הבנתם עד עכשיו, ייצור מעגלים זה לא תהליך פשוט ולא תמיד הכל עובד כמו שהייתם רוצים. תמיד יהיו בעיות ותמיד צריך יהיה לתקן אותן. רצוי להגיע לשורש הבעיה כדי שהיא לא תחזור בפעם הבאה שצריך יהיה לייצר את אותו המעגל. החלפת תנור ההלחמה מבחינתי הוא טיפול בבעיה העיקרית כרגע. שדרוגים למכונת השמה, עם מחסניות מודפסות במדפסת תלת מימד ישפרו את התהליכים מבחינתי, כנראה ימנעו קפיצות של רכיבים שמגיעים לא בגלילים שלמים. לפעמים צריך לעשות שיניים במעגל עצמו כדי לשפר תהליך כלשהו (רכיבים מתנגשים, להחליף לכפתור עם 4 רגליים במקום 2 כדי שיהיה חיבור פיזי חזק יותר וכו').ברוב המקרים הכלים בהם משתמשים לתיקונים זהים לכלים שתראו במעבדות תיקונים לטלפונים סלולריים.
במקרה שלי רוב התיקונים הם סביב ההלחמות הלא טובות. כדי לתקן הלחמה שלא הצליחה אני משתמש בתחנת הלחמה שיש לי או בתחנת אוויר חם מדגם 858D+ של חברת ATTEN:
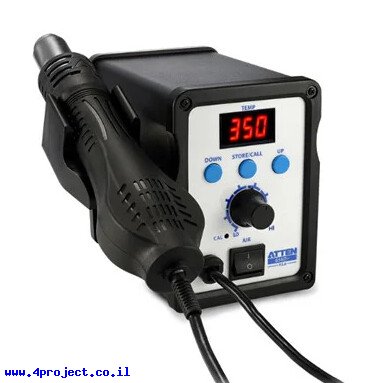
על ידית המכשיר שמים פיה שתוציא את האוויר החם בצורה הרצויה. למשל, כדי לתקן הלחמה אני משתמש בפיה עם צינורית הדקה ביותר שיש לי כדי שאפשר יהיה למקד את האוויר לאיזור הקטן ביותר. לפעמים צריך להוציא רכיב כלשהו שהורכב בצורה לא נכונה (לדוגמה מיקרובקר שהורכב ב-90 מעלות ממה שהוא אמור להיות, כי לא בדקתי את הכיוונים לרכיב זה בשלב תכנות המכונה. דוגמה תיאורטית, עוד לא קרה לי). במקרים כאלה רצוי להשתמש בפיה גדולה יותר כדי שהאוויר החם יגיע לכל הרגליים בו זמנית כדי להמיס את הבדיל ואפשר יהיה להוציא את הרכיב בקלות. יש פיות משוכללות עוד יותר, כך שהאוויר יוצא מארובה ריבועית, כך שרק הרגליים של מיקרובקר יקבלו את מכת החום ולא השבב עצמו.
יש אנשים שמשתמשים באוויר חם גם כדי להלחים מעגלים לטובת אב-טיפוס. אם המעגל פשוט יחסית ויש עליו כמות רכיבים קטנה, זו יכולה להיות אופציה לא רעה בכלל. לא רואה שום סיבה שזה לא יעבוד טוב עם מעגל פשוט כמו זה למשל:
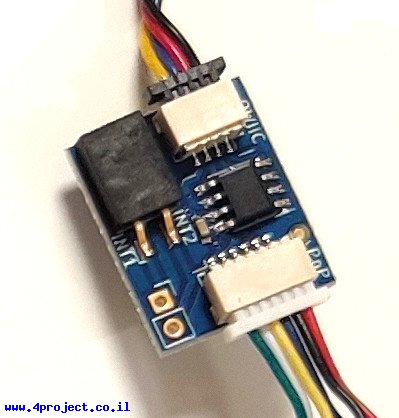
קרה לי כמה פעמים שהרכיבים התהפכו בגלל שהם קפצו במחסנית לפני שמכונת ההשמה לקחה אותם. בשני המקרים הבאים פספסתי את ההתהפכויות לפני שהכנסתי את הכרטיסים לתנור, למרות שבדקתי ויזואלית שהכל נראה תקין. המעגל הזה די צפוף עם הרכיבים והיה קל לפספס את שני המקרים:
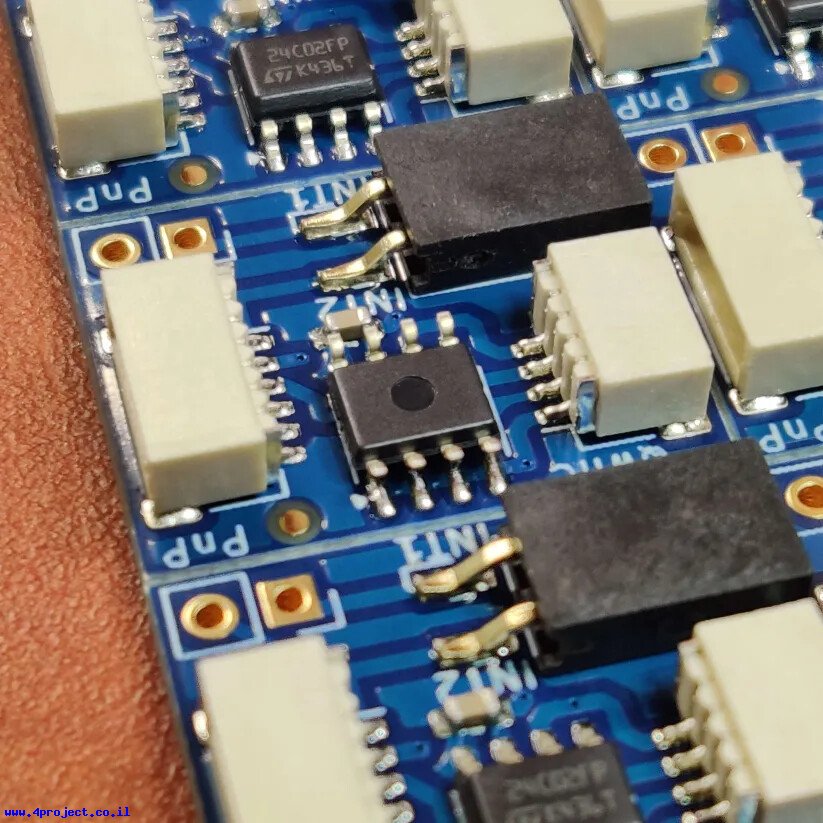
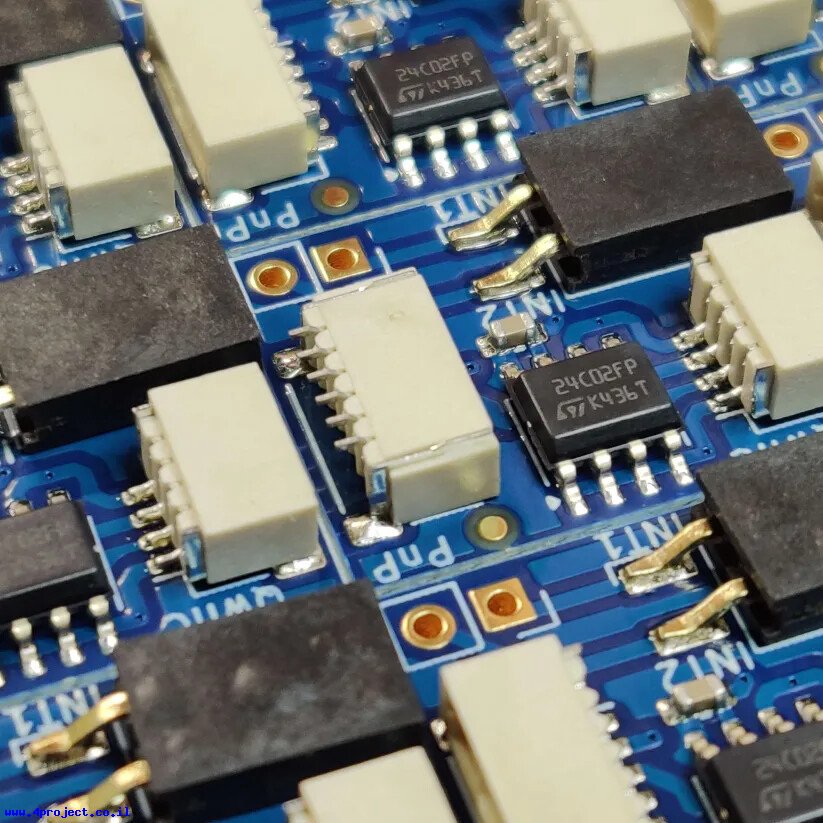
את השבב אפשר להרים בקלות ולהלחים למקום בעזרת אוויר חם. את המחבר יהיה בלתי אפשרי להוציא עם אוויר חם, כי הפלסטיק יימס מהטמפרטורה הגבוהה. במקרים כאלה אפשר להרוס את המחבר ולהלחים אחד חדש. אפשרות אחרת היא להשתמש בפלטת חימום מקדים (Hot plate preheater).
פלטת חימום מקדים, היא כמו שזה נשמע, פלטה שמחממת את המעגל. המכשירים האלה נקראים preheater כי הם אמורים לעזור לחמם את המעגל לטמפרטורה מספיק גבוהה כדי שהבדיל עדיין יהיה מוצק, אבל עם תוספת קטנה של אוויר חם הבדיל יימס בדיוק בנקודה הרצויה. מאוד דומה לאיזורי חימום מתחת למעגל בתנור הלחמה תעשייתי.
אבל רוב הפלטות יכולות להגיע לטמפרטורות מספיק גבוהות כדי להתיך את הבדיל לגמרי, כך שאפשר יהיה להוציא בקלות מיקרובקר עם הרבה רגליים, או מחבר כמו שאני הייתי צריך.
לי אין עדיין מכשיר כזה, אבל הזמנתי בשבוע שעבר את ה"צעצוע" הזה, דגם MHP50 של MINIWARE:
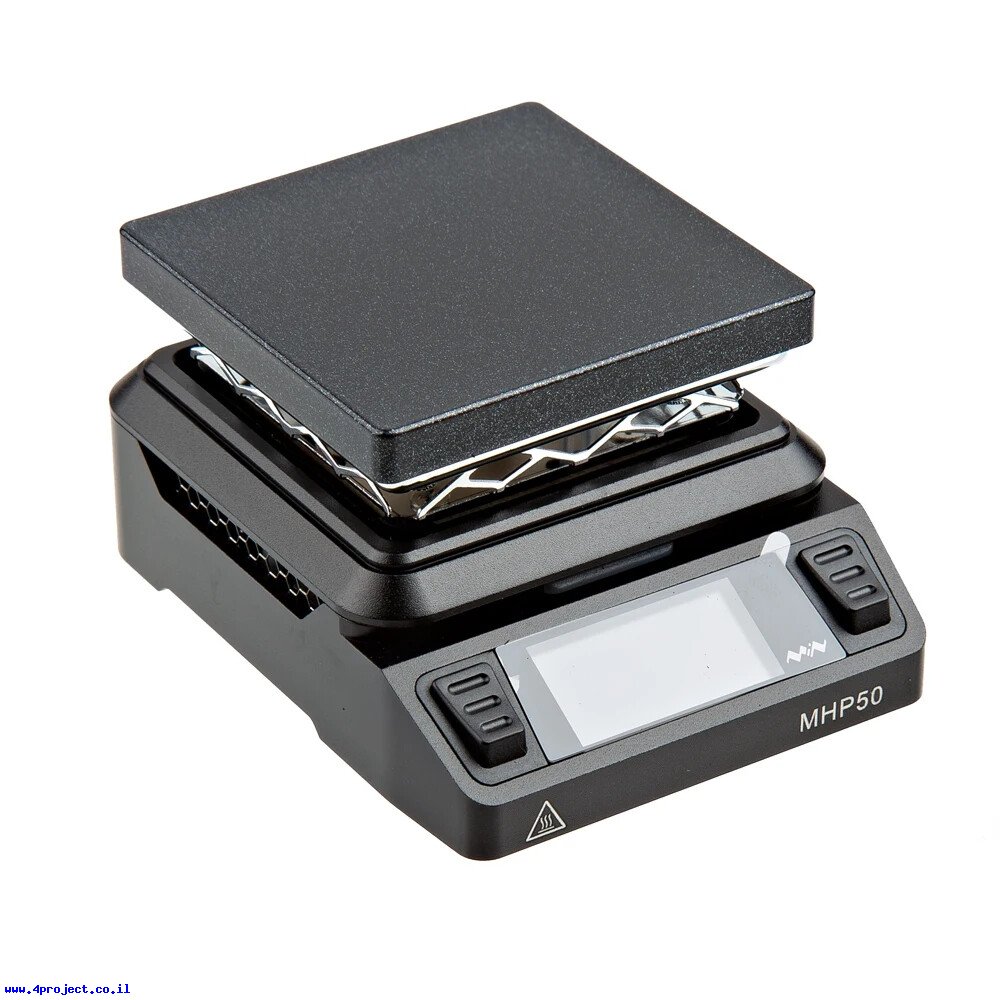
זהו מכשיר קטן, עם לוח חימום בגודל של רק 5x5 ס"מ. אמור להספיק לתיקונים שאני צריך. גובה של המכשיר הוא רק 3.7 ס"מ, כל שהעבודה מעליו עם פינצטה אמורה להיות די נוחה. יש לו אח קטן עם גוף חימום של 3x3 ס"מ, אבל הוא יותר גבוה ממנו ונראה לי שגודל כזה כבר יהיה קטן מדי.
לפי היצרן, הפלטה אמורה להגיע לטמפרטורות של עד 350 מעלות, שאמורים להספיק להלחמות של בדיל נטול עופרת. יש לו מצב עבודה שאפשר להגדיר את פרופיל הטמפרטורה של הבדיל והוא יתנהג כמו תנור הלחמה. מהסרטונים שראיתי ביוטיוב אנשים פשוט מפעילים אותו על 300 מעלות, מצמידים את המעגל לפלטה, מחכים שהבדיל יימס ומורידים את המעגל לקירור. אם המעגל גדול יותר מהפלטה, אז פשוט מזיזים אותו כדי שאיזור אחר יעבור הלחמה. נשמע כפתרון מעולה לשלב אב-טיפוס הראשוני.
מכשירים מקצועיים יותר לרוב גדולים יותר כדי לתמוך במעגלים גדולים. ראיתי גם 20x20 ס"מ וגם 30x30 ס"מ. יש מכשירים שבמקום לחמם פלטה, הם זורקים אוויר חם למעלה כדי שאפשר יהיה לחמם מעגלים עם רכיבים גם בצד התחתון.
וגם כאן, כמו בשלב ההלחמות, לפעמים הכי פשוט זה להשתמש במלחם. הנה סרטון נוסף המדגים הסרה של רכיבי SMD והלחמה של אחרים:
מה עוד הייתי רוצה לטובת ייצור מעגלים?
יש עוד המון מכונות שונות שמשתמשים בהם בתהליכי ייצור מעגלים. חלקם נועדו לשיפור התפוקה, חלקם לאוטומציה של תהליכים וגם בדיקות. לא אכנס לזה בפוסט זה כי אין לזה סוף.אם לחשוב על היכולות שאין לי עדיין לטובת ייצור, שהייתי מאוד רוצה שיהיו, זו אפשרות של הלחמת רכיבי PTH. כאלה שמולחמים בשיטה הישנה שבה מכניסים רגלי הרכיב לחור, מצמידים מלחם ומוסיפים בדיל:
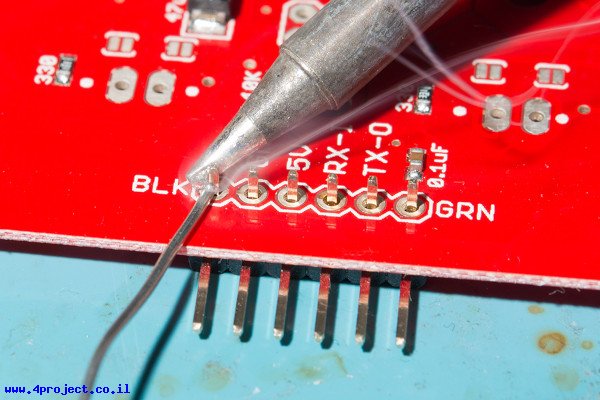
לא את כל הרכיבים אפשר להחליף ברכיבי SMT. יש את הממסרים והרבה סוגי מחברים שעדיין מולחמים בצורה זו ואין להם אלטרנטיבה אחרת. גם אם יש אלטרנטיבה, כמו המחברים של 2.54 מ"מ למשל, יש דגמים גם להלחמת PTH וגם SMT, ה-SMT דורש יותר מקום על המעגל, יהיה פחות חזק מכנית וגם לרוב יהיה יקר יותר בהשוואה למקביל שלו להלחמת PTH.
יש כמה שיטות הלחמה של רכיבי PTH בצורה אוטומטית, אבל הפשוטה והזולה ביותר היא רובוט הלחמה, שעושה בדיוק את אותו הדבר שהאדם עושה, אבל לא מתעייף.
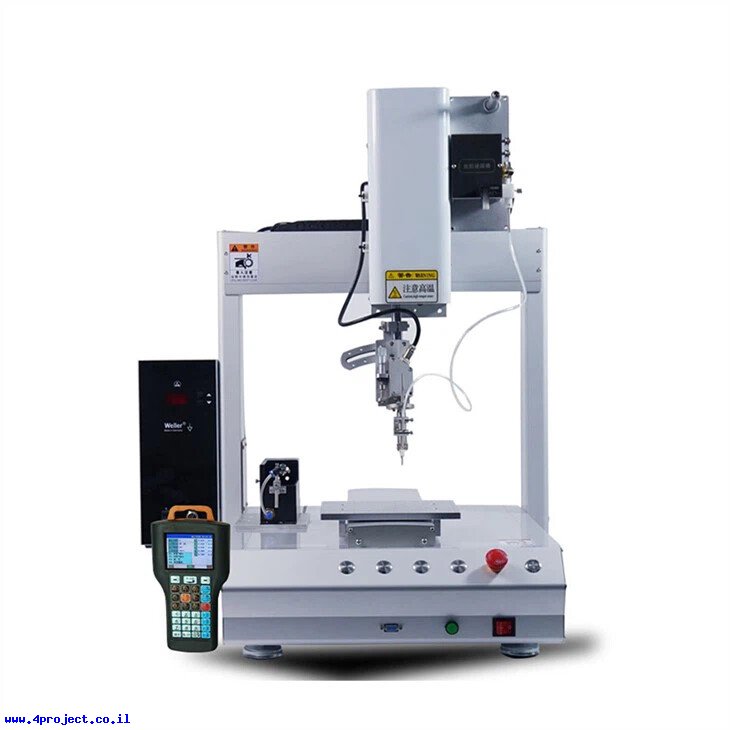
זו למעשה פלטפורמה לתנועה בצירים X/Y/Z וסיבוב ראש, אליו מחוברת ידית של מלחם. מתכנתים להם את התנועות שצריך לבצע, ופשוט חוזרים על אותה התוכנית שוב ושוב. מכונה כזו לא מהירה במיוחד, אבל אחרי שמתכנתים אותה כמו שצריך, יכולה לחסוך הרבה עבודה ידנית.
הנה דוגמה לרובוט כזה בפעולה:
יש לכם הערות או שאלות? מתעניינים בתחום ייצור מעגלים?
מוזמנים לשאול ולהגיב כתגובה לפוסט בפייסבוק.